|
Method
of making Steel in the style of Damascus
written
in 1771
by
Jean Jacques Perret
Updated November
4th, 2000
|
Damascus
Steel ? / History / JJ Perret

|
The following text is a translation made by
Mister Bernard Levine of the 29th chapter of the famous
Jean Jacques Perret book : L'Art du Coutelier
"The Art of the Cutler". His translation is enlighted
by some pictures from the J.J. Perret book.
You will find the original translation at :
http://207.221.52.114/p29-dama.txt
Mister Bernard Levine home page is at : http://www.knife-expert.com
|
Introduction notes from Mister Bernard Levine
THE ART OF THE CUTLER
In years past the late Tom Sewell wrote extensively in these
pages about Jean Jacques Perret, the 18th century French master
cutler and surgical instrument maker who was, very likely, the
greatest knifemaker who has ever lived. Perret was the man who,
beginning as a teen-ager, worked in and learned the trade secrets
of every cutlery center in France. Perret was the man who did
a full course of study at medical school, in order to improve
the quality of his surgical instruments. Perret was the man who
said that a practical test of a cutler's skill was for him to
draw out from bar stock a steel wire 6-1/2 inches long and 1/6
inch in diameter, and then to drill a 1/12 inch diameter hole
through this wire with his breast drill -- the long way. And Perret
was the man who, in 1771, wrote and illustrated what is still
the finest knifemaking how-to book ever published.
Perret's book is called L'Art du Coutelier -- "The Art of the
Cutler". It includes three large thick volumes, the latter two
dealing with surgical instruments, and all three illustrated with
hundreds of splendid engravings.
Every aspect of knifemaking is covered, from engineering design
and materials preparation, to the art of selling and shop management.
Of course some of the material is obsolete, such as the parts
pertaining to pre-Revolutionary French business practices, although
even here we might learn a thing or two. Most of Perret's technical
material, however, is as valid today as it was when it was published,
over 220 years ago.
Today we might use power saws instead of hand saws to cut ivory,
horn, or wood handle slabs, but the principles of sawing these
materials to achieve stable dimensions and attractive grain have
not changed at all. Today we might use refined steel alloys that
Perret never dreamed of, and we might buy ready-made drill bits
and lathe cutters where Perret made his own, but when it comes
to shaping those alloys and using those tools, Perret could teach
most of us a lot more than we could teach him.
I imagine that Perret would be pleased to see the current popularity
of damascus steel in hand-made knives today, both in America and
in his native France. Perret made many damascus knives and swords,
as did other Parisian cutlers both before him and after him. Some
of his contemporaries even made fake damascus, and Perret exposed
their shady methods.
As far as we know, no one in Europe at that time made eastern
damascus, what we now call Wootz. However Perret and his fellow
European cutlers were familiar with that material, and recognized
that it was different from their own product. Perret called it
le Damas naturel "natural damascus." Since we now know that the
pattern in Wootz forms spontaneously, this seems to be a very
appropriate name.
Damascus steel was such a popular topic in Perret's own day that
he felt called upon to include an entire chapter on its fabrication
in The Art of the Cutler. This is Chapter 29, "Maniere de faire
l'Acier facon de Damas" ("Method of making Steel in the style
of Damascus"). Here is a somewhat loose translation. [Note: the
"inches" (pouces) referred to are French Royal inches, which are
1/12 longer than our English inches.]
|
Method
of making Steel in the style of Damascus
Jean Jacques Perret,
1771
We
might have discussed this steel in the chapter on materials, because
it is one. However, since it is not appropriate for fine cutting
edges, we believed it our duty to treat it separately, although
this steel does serve very well for making table knives.
This material, which closely imitates "natural" damascus, can
become costly. This is because of the time required [to make it],
as well as because of the quantity of coal one must employ, and
the diminution of the metal [during fabrication]. If one wishes
to make 3 pounds weight, it is necessary to start with 6 pounds
weight of raw material.
Start out by forging six thin plates of iron, exactly identical
in all respects. Let us suppose that they are each a pouce (an
inch) wide, a ligne (1/12 inch) thick, and 12 inches long. Then
forge five thin plates of steel, identical in form to those of
iron, making in total eleven thin plates. The more plates one
uses, the finer the material will be. Stack these plates one atop
another, but be sure to put each steel plate between two of iron,
which means starting and finishing with an iron plate. This is
how it must be done, no matter how many plates one uses. This
should become clear from Figure 1.[In
the figure] each thin plate is numbered from 1 to 11, and under
each number one sees a letter that designates the material: A
for Acier (steel) and f for fer (iron).
|
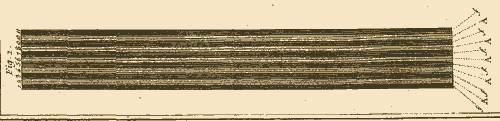
|
Once
all this is properly arranged, grasp all the plates with a tongs.
Clamp the handles of the tongs with an "S" as shown in Chapter
12. Place this stack in a moderate fire. Raise the temperature
so that all the plates heat uniformly through and through, but
do not allow any of them to burn. To this end, turn the packet
often in the fire, without removing it, and then let it rest in
the fire a little while. The plates that are in the center will
not heat up as fast as those on the outside, mainly because the
latter receive heat directly from the coals, while those in the
center receive none except from their neighbors. Finally, when
the whole thing is uniformly hot, moderate the pumping of your
bellows, "sand" [i.e. dust with flux] the material at least twice
after each heat, and forge it squarely, working it down to a thickness
of 8 or 9 lignes (2/3 to 3/4 inch) on a side. After this is done,
heat the material up to a bright red, but not quite white, and
clamp one end in the vice, as shown in Figure 2.
|
|
With
stout tongs twist the material from one end to the other, as evenly
as possible, so that it resembles a screw, as shown in Figure 3. |
|
Now
it is necessary to flatten and forge it out to a width of 9 lignes
(3/4 inch) and a thickness of 3 lignes (1/4 inch). After this fold
it in two [the long way], in the manner shown in Figure 4. |
|
All
this work, up until now, is for nothing other than to form a strong
tenacious covering, such that no effort or power can break it apart.
The plates of soft iron are thoroughly welded, married, and entwined
with the ones of steel, forming together an extremely tough material,
more tough than either component. The iron and steel are well bonded
together, and the individual particles of each are very small. However,
it is not possible for this material to be given a really fine cutting
edge. The "veins" of iron that wind throughout prevent it. Make,
therefore, a thin plate of good German steel 9 lignes wide, Figure
5, (that is, the same width as the covering), and at the very most
2-1/2 lignes thick; its length must be equal to that of the covering
which has been folded in half. |
|
Put
this steel plate between the two sides of the covering. Then forge
weld the whole assembly. Do not overheat the billet. Avoid striking
it too hard. Use only the face of the hammer. Shape the surfaces
squarely, so that the steel remains always in the center of the
billet, because upon this depends the quality of the cutting edge.
Then draw out the billet to the length and width which you require.
A
blade made from damascus material can never break, save only by
forcefully bending it back and forth many times. Therefore it
makes a strong knife. And if one tempers this knife to the color
of red copper, after having hardened it at a cherry color, one
would be able to cut iron very readily with it, without the edge
chipping, provided however that one made the edge a bit thick
and rounded. But if one is making this knife to cut food at the
table, and one does not wish to show off with it, one should give
it a little finer cutting edge, which requires no more than tempering
it to a gold color, instead of red copper color. Then one will
have a good tool which will cut well, and which will keep a good
edge for a long time.
If
men did not seek so often to pinch pennies on that which is useful,
all the while making huge expenditures on useless ornamentation,
then instead of having a sheath knife worn at one's side whose
blade cost not even 40 sols (five-cent pieces), but whose mounts
cost 60 livres (pounds); one might instead have a blade which
cost 60 livres, in mounts which cost 40 sols. Nothing can make
a better blade for a Couteau de chasse (literally a "hunting knife,"
but actually a hunting sword, or hanger) than damascus material
just as I have described. Its utility is found in the implement's
requirements [chopping through bones]. The object for which this
material is nearly indispensable is the Damas a decoler, the damascus
beheading sword.
|
|
Figure
6 represents the one which is used by the Honorable Mr. Sanson.
[Charles Henri Sanson, 1740-1795, was the public executioner in
Paris. He was to preside over the execution of Louis XVI in 1793.]
His sword is 9 inches long in the handle, between A and B, and
3 feet in the blade (3 French feet, or 39 English inches). The
width is, at the base of the blade, 2-1/2 pouces, tapering very
slightly to C. Its thickness below B is three lignes (1/4 inch),
but it thins steadily right up to the point, where it is but one
ligne (1/12 inch) thick at C. This makes it more flexible than
an epee. It is double-edged and does not have a sharp point. On
the contrary it is well-rounded, because a sharp point can get
stuck in the vertebrae. Being rounded and well polished, it slides
and cuts easily. Its edges are the same on both sides, and it
is as keen as a fine pen knife that is used for sharpening quills.
It is necessary that it be polished the long way on a polishing
wheel which is at least an inch wide, taking careful precautions
not to injure oneself. It must be honed on a razor stone, or else
on a fine-grained Levant stone. This is what I have always done.
On
might well think that forging damascus material and forging pure
steel are much the same thing; in either case one must treat them
with "art" in order to preserve their "virtue." However, it is
necessary to forge damascus with a great deal more care. Once
it is completely welded throughout, it is not necessary to give
it additional welding heats. Most of all, in the final heats,
do not heat it past cherry color, and in the last heat past the
color of bronze. Then hammer the material well until it is cold.
One need not be ashamed to use files to shape it. File it without
additional reheating.
The
hardening, which gives the final touch of quality to this material,
must be done with all possible attention. For such a piece as
this, do not use just any forge. Instead light, on the ground,
a charcoal fire of sufficient size to surround and heat the entire
piece. When the fire is burned down to coals, put the piece in
the center and cover it completely with hot coals. Do not use
a bellows, but only agitate the air with a piece of cardboard,
or something equivalent. Pay attention that the blade heat uniformly
throughout. As soon as it has reached a bright cherry color, plunge
it into a big bucket of water, or a big cask of water if the hunting
sword or saber is three feet long.
Some
people brag about certain other hardening methods which, if truth
be told, do not have anything wrong with them. However, since
we discussed this subject elsewhere, I will not say any more about
it here. I will merely point out that with proper attention paid
to forging the steel, and to the degree of heat in the hardening,
plain cold water is worth more than all the ingredients which
one might add to contaminate it.
When damascus is polished, the eye of the connoisseur can judge
if it is really damascus, because one can distinguish the flowing
whitish veins of the iron from the bluish veins of the steel.
However, for giving effective color to damascus, and to make those
veins stand out, pour a little eau forte [dilute nitric acid]
on to the piece (completely finished). Spread it out over the
entire length of the blade with a feather. Leave the acid on the
blade for the space of 6 or 7 minutes. After this time rinse the
blade with clear water, dry it, and you will find it damassee,
which is to say one may readily distinguish the veins of steel
from those of iron.
In
general, steel is subject to having closely spaced veins. [This
is a feature of shear steel, the best type available in 18th century
France.] In consequence one can be fooled, and buy steel blades
which are not damascus, because it is only necessary to wipe a
knife, a razor, &c, with some acid, to give it the color of damascus.
However, one can judge [real damascus] by the regularity of the
"flowers," and by the veins of iron which flow with a sort of
regular symmetry. On can also recognize damascus steel, worked
the way we have described, by its being largely forged to shape,
and because its veins are small and evenly distributed, and because
the metal is of good quality.
I
have seen some hunting swords which were sold as damascus, but
which I suspected not to be, in part because the blackish veins
were too deep, and in part because their edges would not cut iron.
Indeed their edges were so blunt and ill-shaped that they would
not even cut wood. I tried to discover the method of "damascening"
blades as boldly as these. After several trials I took a blade
of polished steel and I covered it with a coating of wax, which
I let drip from a lighted candle. I spread the wax evenly over
the entire surface. Then I drew a quantity of lines in the wax,
using a steel scribe which served me as a pencil. After that I
poured some acid on the wax. I allowed it to bite or dissolve
the steel which my "pencil" had uncovered for about an hour. I
then cleaned it off, and found that I had discovered the whole
secret.
Figure 7 shows a hunting sword with blade made of damascus.
|
|
|
|
|